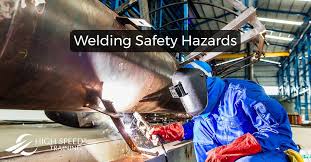
Best practices to avoid common welding hazards
Welding is an essential skill used in various industries, from construction to manufacturing. However, it comes with its fair share of hazards. From burns to toxic fumes, welders face risks every day on the job. Fortunately, by following best practices, you can significantly reduce the likelihood of accidents and injuries. In this blog, we'll explore the most common welding hazards and practical tips to stay safe.
Welding Hazards: Risks and Precautions
Welding involves joining metal pieces by melting them together, often using intense heat and electrical currents. While it's a valuable technique, it also poses several dangers to those involved. Some common hazards include:
- Electric Shock: Welding equipment operates on high voltage, putting workers at risk of electric shock.
- Fumes and Gases: The process of welding produces fumes and gases that, if inhaled, can cause respiratory issues and long-term health problems.
- Eye Injuries: Intense light and radiation generated during welding can damage the eyes, leading to conditions like arc eye and cataracts.
- Burns and Fires: Welding involves working with hot metals, sparks, and open flames, increasing the risk of burns and fires if proper precautions aren't taken.
What are the best practices that welders can adopt to avoid common welding hazards and ensure their safety while on the job?
1. Training and Education:
- Before starting any welding work, it's essential to undergo comprehensive training on safe welding practices. This training should cover topics like hazard identification, proper equipment usage, and emergency procedures.
- Regular refresher courses and updates on safety protocols should be provided to ensure that welders stay informed about the latest best practices.
2. Personal Protective Equipment (PPE):
- Wearing appropriate PPE is non-negotiable when it comes to welding safety. This includes items such as welding helmets, gloves, goggles, and flame-resistant clothing.
- Ensure that PPE fits properly and is in good condition to provide maximum protection against sparks, heat, and radiation.
3. Ventilation and Air Quality:
- Adequate ventilation is crucial for removing welding fumes and gases from the work area. Work in well-ventilated spaces whenever possible, or use local exhaust ventilation systems to capture fumes at the source.
- Monitor air quality regularly to ensure that exposure to harmful substances like manganese, chromium, and nickel is minimized.
4. Fire Prevention:
- Welding involves high temperatures and sparks, making the risk of fire a constant concern. Keep a fire extinguisher nearby at all times and ensure that it is regularly inspected and maintained.
- Clear the work area of flammable materials and use fire-resistant barriers or blankets to protect nearby surfaces from sparks and heat.
5. Electrical Safety:
- Inspect welding equipment regularly for damaged cords, frayed wires, or other potential electrical hazards. Never operate defective equipment.
- Ensure that welding machines are properly grounded to prevent electrical shocks. Avoid contact with wet surfaces while welding to reduce the risk of electrocution.
6. Safe Work Practices:
- Maintain a clutter-free work area to prevent trips, slips, and falls. Keep cables and hoses neatly arranged and secured to avoid accidents.
- Never weld in confined spaces without proper ventilation and safety measures in place. Always have a spotter or observer nearby, especially when working at heights or in hazardous conditions.
7. Preventive Maintenance:
- Regularly inspect and maintain welding equipment to ensure that it operates safely and efficiently. Replace worn-out parts, such as nozzles and tips, as needed.
- Develop a preventive maintenance schedule for welding machines and tools, and adhere to it strictly to prevent unexpected breakdowns or malfunctions.
8. Stay Informed and Aware:
- Keep up-to-date with industry regulations, safety guidelines, and best practices related to welding. Attend seminars, workshops, or online courses to expand your knowledge and skills.
- Encourage open communication about safety concerns and incidents in the workplace. Report any hazards or near misses promptly to prevent future accidents.
In conclusion, prioritizing safety through training, proper equipment use, and adherence to safety protocols is paramount in mitigating welding hazards. By implementing these best practices diligently, welders can significantly reduce the risk of accidents and create a safer work environment for themselves and their colleagues.